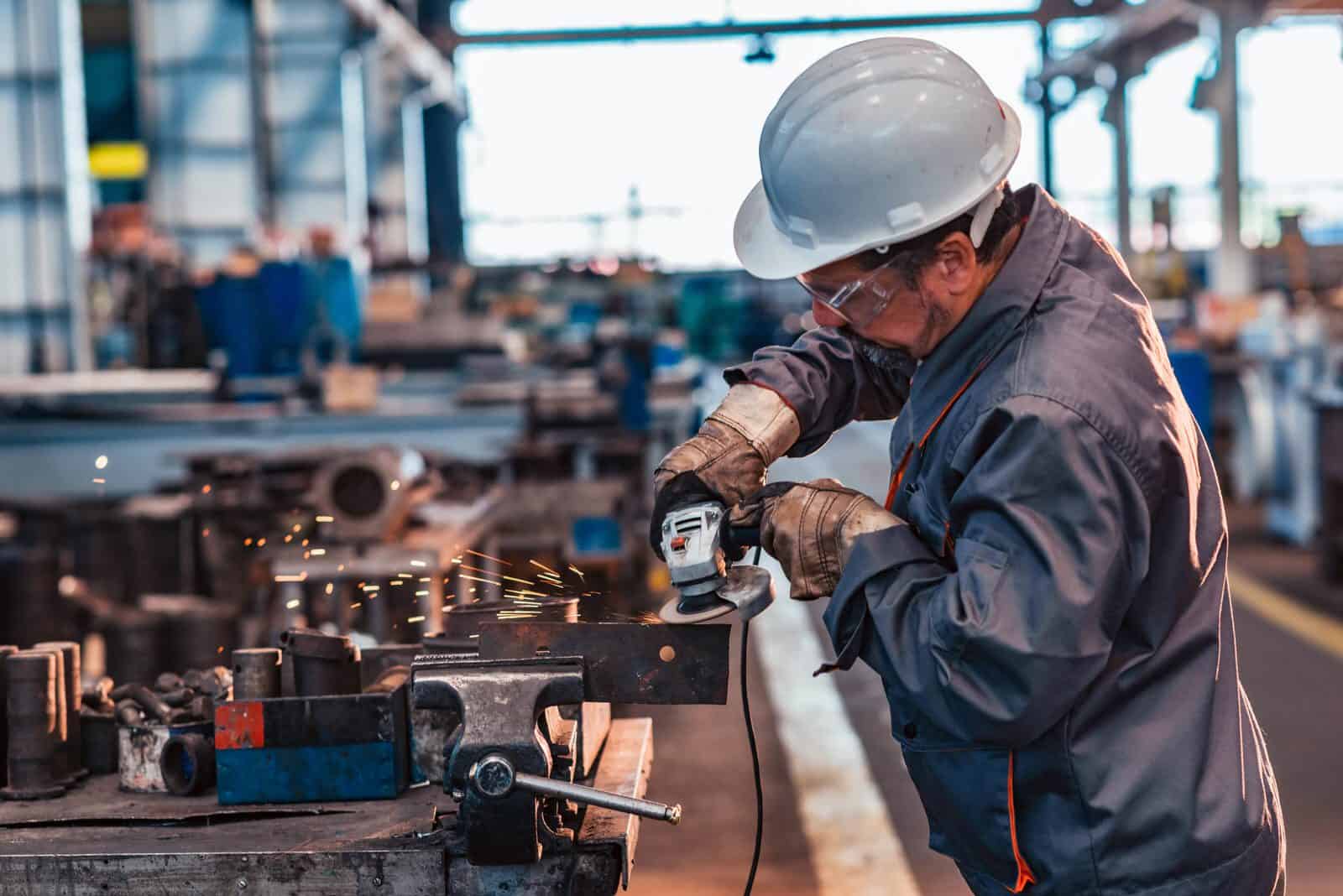
Maintenance Strategies
There are four main maintenance strategies; REACTIVE, PREVENTATIVE, PREDICTIVE, RELIABILITY. This blog describes each type but in reality most companies must blend these together. This is because every company will have a range of assets from low value and low importance, to high value and strategic assets.
Deciding how to maintain an asset is often by intuition and experience. Risk is a key factor in determining how asset maintenance should be performed. For example, a washroom dyer can be repaired once a failure occurs. It would be easy to live with a broken dryer for a few days. A factory compressor could stop all production work, so this asset is far more ciritical. Maintenace could involve preventative and possibly some predictive maintenance routines for a compressor. For large companies with many assets, risk assessment tools will help to indentify and prioritise assets.
REACTIVE
As it suggests this is reacting to a fault or breakdown once it occurs. This is the simplest form of maintenance and suitable for low value, easily replaced or repaired equipment. This type of maintenance is very cheap because essential nothing is done until the failure. Problems are expected when reactive becomes the norm, or the culture within an organisation. Considering higher value and more critical assets, this strategy proves to be more expensive. Allowing assets to breakdown increases the number and value of parts required aswell as extending the repair time. Unplanned shutdowns cause a loss of production which can dramatically increase costs for the company.
Preventative
Preventative maintenance is a strategy to apply to more valuable and important assets within your company. To keep assets running, regular maintenance work is scheduled at timed intervals. Preventative maintenance work greatly reduces the chance of breakdowns. Regular walk-arounds and inspections also highlight issues early before they become problems.
Preventative maintenace includes replacing wear parts, changing filters, inspections and testing. The works orders repeat at regular intevals such as daily, weekly, monthly etc.. It is important to note manufacturers maintenance manuals which normally provide the time intervals and tasks.
Predictive
Predictive maintenance takes preventative one step further. As explained, preventative is based on fixed time intervals to perform a works order. In reality, exactly how long an asset is operating will detemine when some work should be performed. For example, run hours of machine or cycles of an operation may vary with demand. It may also be that poor installation, poor quality parts, or the type of work affect the life cycle of spares and systems.
To improve reliability and reduce costs, a predictive strategy sets the works order interval based on other factors. These factors could be run-hours, or cycles of machine and can include measurements such as temperatures or pressures.
For example, a bearing in production machinery can be changed every 6 months on a preventative maintenance routine. However, since a bearing will heat up more excessive wear, temperature can be used as a parameter to predict when the bearing is about to fail. Instead of a works order every 6 months to change the bearing, predictive maintenance requires regular temperature measurements of the bearing. This information has to be collected on a regular basis and logged. By monitoring the data any increase in temperature can be observed, which will trigger the time to change the bearing before it fails. This could be earlier or later than the fixed time interval. But in either case, it can reduce costs.
Predictive maintenance can use many types of sensors connected to to assets. Using technologies such as as Internet of Things (IoT) data collection can be automated.
Reliability
Reliability centred maintenance is the most complex approach to maintenance. In predictive maintenance some assumptions are made about when a failure will occur. An example would be that a bearing will fail shortly after it reaches 80 deg C, or a seal will fail after 10,000 cycles.
Reliability centred maintenance considers that all machines are different. Different in the sense that they are not linear due to a variety of minor differences in their construction and installation. In order to perform Reliability centred maintenance, the maintenance team must analyse each machine separately. Consideration is made for all risks and factors that can affect the asset. This is only possible once the team have mastered the other maintenance techniques and have an in depth and analytical understanding. This is not commonly used in most industries and most CMMS systems don’t cater to this complexity.